Weltweit erste agile Batteriezellfertigung eröffnet
Um Batteriezellen künftig flexibler herstellen zu können, haben Forschende eine agile Batteriezellfertigung aufgebaut. Auf Basis einer hochflexiblen roboterbasierten Automatisierung haben sie einen Flexibilitätsgrad erreicht, der bisher nur in der manuellen Zellfertigung realisierbar war. Dies ermöglicht es Unternehmen, sich schneller an neue Technologien und volatile Märkte anzupassen und kann die Wettbewerbsfähigkeit von Deutschland als Industriestandort stärken.
17.10.2024
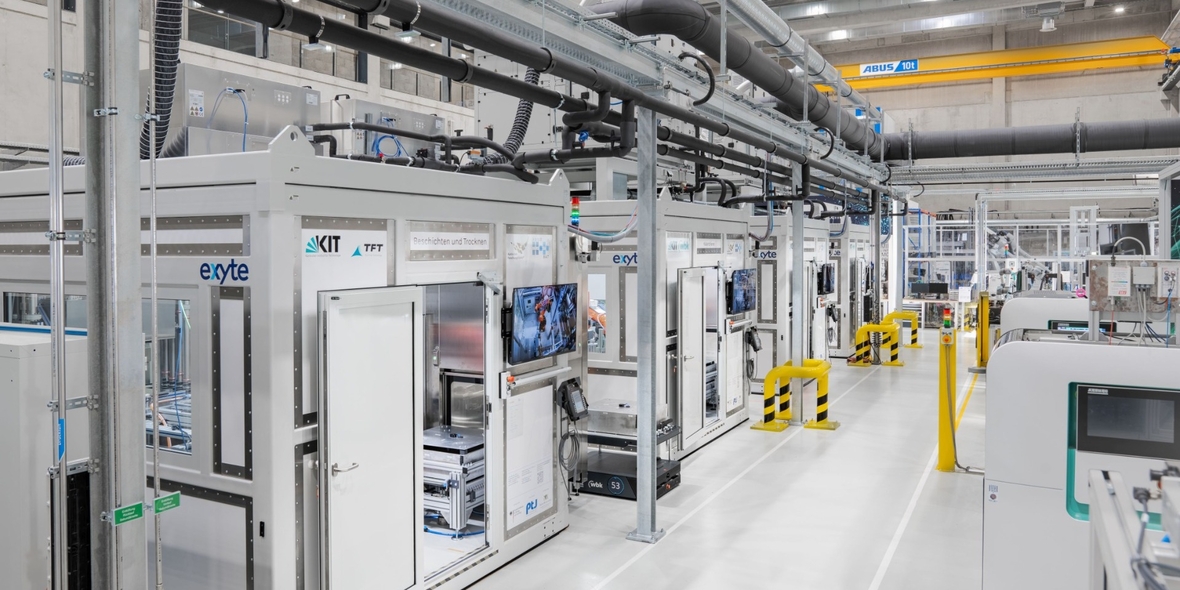
Nach Angaben des Bundesministeriums für Wirtschaft und Klimaschutz gewinnen Batteriezellen als vielseitige und effiziente Energiespeicher zunehmend an Bedeutung. Sie spielen eine entscheidende Rolle bei der fortschreitenden Elektrifizierung des Verkehrs. Für produzierende Unternehmen ist diese Schlüsseltechnologie von hoher strategischer und wirtschaftlicher Bedeutung. Derzeit wird die Nachfrage vor allem durch kostengünstige Massenproduktion in Asien und Nordamerika bedient, was auch Auswirkungen auf den Maschinen- und Anlagenbau hat. „Wir haben in Deutschland nicht die Voraussetzungen, um in der rein kostengetriebenen Massenfertigung von Zellen und dem dazugehörigen Maschinenbau wettbewerbsfähig zu sein“, sagt Professor Jürgen Fleischer, Leiter des wbk Institut für Produktionstechnik am KIT. „Die Eröffnung der weltweit ersten agilen Batteriezellfertigung in der Karlsruher Forschungsfabrik zeigt, wie wir uns mit einer hochflexiblen und ressourceneffizienten Produktion vom Weltmarkt differenzieren und gezielt das margenstarke Premiumsegment und Nischenmärkte adressieren können.“
Flexible und ressourceneffiziente Batteriezellfertigung
Für die Batteriezellfertigung entwickelten die Forschenden des KIT gemeinsam mit der Firma Exyte spezielle Roboterzellen. „Diese stellen eine Weltneuheit auf dem Gebiet dar. Sie dienen als lokale Trockenräume, auch Microenvironments genannt, zum Schutz der feuchtigkeitsempfindlichen Batteriematerialien“, so Fleischer. Im Vergleich zu herkömmlichen Trockenräumen ist das zu entfeuchtende Raumvolumen deutlich geringer. Dadurch ist diese Technologie besonders energieeffizient. In der Karlsruher Forschungsfabrik des wbk bilden vier solcher Mikroumgebungen mit den entsprechenden Prozessmodulen die physikalische Basis für die agile Batteriezellfertigung.
Zusätzlich haben die Projektbeteiligten einen „digitalen Zwilling“, ein virtuelles Modell des Produktionssystems, erstellt. Damit können die Wissenschaftlerinnen und Wissenschaftler softwaregestützt Skaleneffekte durch die Vervielfältigung einzelner Mikroumgebungen analysieren und produktionstechnische Parameter wie die optimale Losgröße bestimmen. Diese Simulation dient auch der Produktionsplanung in der agilen Batteriezellfertigung. Die reale Anlage ist mit einer Datenbank verknüpft, so dass künftig alle Prozesse mit Hilfe künstlicher Intelligenz optimiert und angepasst werden können.
Enge Kooperation zwischen Wissenschaft und Industrie
Im Forschungsprojekt AgiloBat haben Wissenschaftler:innen gemeinsam mit mittelständischen Maschinen- und Anlagenbauern eine innovative Batteriezellfertigung entwickelt. Ziel ist es, diese Unternehmen in die Lage zu versetzen, gemeinsam wettbewerbsfähige Anlagentechnologien entlang der gesamten Prozesskette anzubieten. Das vom KIT bereitgestellte Prozesswissen zur Flexibilisierung und Modularisierung der Anlagentechnik ermöglicht es den beteiligten Unternehmen, Batteriezellen künftig variantenflexibel, ressourceneffizient und automatisiert herzustellen. Zudem können sie neue Materialsysteme im industriellen Umfeld mit geringen Materialmengen erproben. Die neu entwickelte Infrastruktur ergänzt die 2011 am KIT etablierte Forschungsinfrastruktur im Bereich der Batteriezellfertigung.
Weitere Informationen zu AgiloBat
Im Forschungsprojekt AgiloBat kooperieren Wissenschaftlerinnen und Wissenschaftler aus sieben Instituten des KIT mit Partnern des Zentrums für Sonnenenergie- und Wasserstoff-Forschung Baden-Württemberg und des Fraunhofer-Instituts für Chemische Technologie. Darüber hinaus sind mehrere Unternehmen aus dem Maschinen- und Anlagenbau beteiligt, darunter die Coperion GmbH, die SAUERESSIG Group, die Schunk Group, Herrmann Ultraschalltechnik GmbH & Co. KG, Siemens AG, DEHOF ingenieur+technik und Exyte Technology GmbH.
Das Projekt wird vom Bundesministerium für Bildung und Forschung mit 14,5 Millionen Euro und vom Ministerium für Wissenschaft, Forschung und Kunst Baden-Württemberg mit 4,5 Millionen Euro gefördert. (kla)
Als „Die Forschungsuniversität in der Helmholtz-Gemeinschaft“ schafft und vermittelt das KIT Wissen für Gesellschaft und Umwelt. Ziel ist es, wesentliche Beiträge zu den globalen Herausforderungen in den Bereichen Energie, Mobilität und Information zu leisten. Dafür arbeiten rund 10.000 Mitarbeiterinnen und Mitarbeiter in einem breiten Fächerspektrum aus Natur-, Ingenieur-, Wirtschafts-, Geistes- und Sozialwissenschaften. Seine 22.800 Studierenden bereitet das KIT durch ein forschungsorientiertes Studium auf verantwortungsvolle Aufgaben in Gesellschaft, Wirtschaft und Wissenschaft vor. Die Innovationsaktivitäten am KIT verknüpfen Erkenntnisse mit praktischen Anwendungen, die dem gesellschaftlichen Nutzen, dem wirtschaftlichen Wohlstand und dem Erhalt unserer natürlichen Lebensgrundlagen dienen. Das KIT gehört zu den deutschen Exzellenzuniversitäten.