Ressourcenschonend: Kalksteinmehl statt Wasser in der BMW-Lackiererei
Die BMW Group setzt sich intensiv für nachhaltige Produktionslösungen ein, um sich für die Zukunft zu rüsten. Die Lackieranlagen in den BMW Werken Dingolfing und Regensburg werden in Kürze vollständig auf das Trockenabscheidungsverfahren mit Kalksteinmehl umgestellt. Durch die Umstellung werden jährlich 17 Millionen Liter Wasser und rund 17.400 Megawattstunden Energie eingespart.
24.08.2024
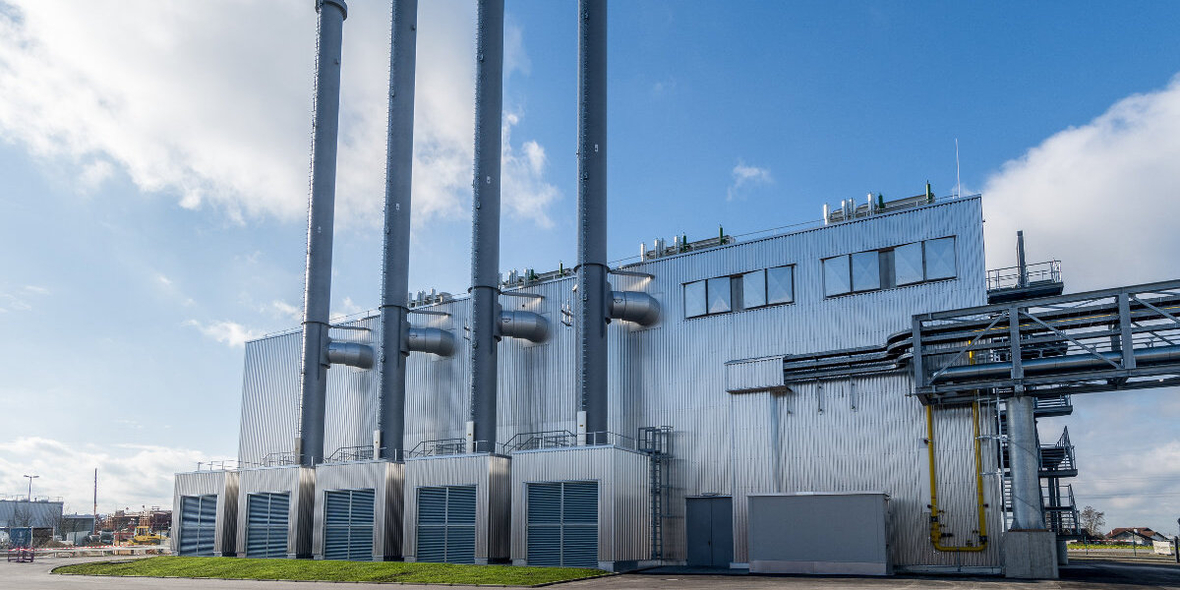
Mit diesen Maßnahmen setzen die BMW Group Werke Dingolfing und Regensburg neue Maßstäbe im Ressourcen- und Umweltschutz. Die Lackiererei in Dingolfing ist die erste im weltweiten Produktionsverbund des Unternehmens, die komplett auf die Trockenabscheidung mit Kalksteinmehl umgestellt wurde. In nur zwei Jahren wurden alle vier Lackierstraßen bei laufendem Betrieb modernisiert. Derzeit läuft die Umstellung im Werk Regensburg: Eine der beiden Basislacklinien wurde im Januar 2024 umgerüstet, die zweite Linie folgt im August 2025.
Da die Lackierung der energieintensivste Schritt in der Fahrzeugproduktion ist, haben diese Maßnahmen einen signifikanten Einfluss auf die CO2-Bilanz beider Werke. Anton Kronseder, Leiter der Lackiererei in Dingolfing, sagt dazu: „Mit der Umrüstung des Lackierverfahrens rücken wir wieder einen Schritt näher an das Ziel der BMW Group, die CO2-Emissionen über den gesamten Lebenszyklus eines Fahrzeugs bis 2030 um 40 Prozent zu reduzieren.“
Durch das neue Verfahren werden in beiden Werken insgesamt 17 Millionen Liter Wasser pro Jahr eingespart, was dem Jahresverbrauch von fast 100 vierköpfigen Familien entspricht. Der durch die Trockenabscheidung ermöglichte Umluftbetrieb reduziert den Heizenergiebedarf um 17.400 Megawattstunden pro Jahr und damit den CO2-Ausstoß um mehr als 5.000 Tonnen. Zudem wird das als Bindemittel eingesetzte Steinmehl anschließend recycelt und in der Baustoffindustrie wiederverwendet.
Obwohl die Lackieranlage in Dingolfing die erste war, die auf diese Technologie umgestellt wurde, fand der erste konzernweite Einsatz der neuen Technologie in der Oberpfalz statt. Bereits 2010 hatte das Werk Regensburg den Klarlackauftrag der beiden Lackierstraßen erfolgreich umgestellt. „Das war nicht nur der Ersteinsatz der Trockenabscheidung mit Steinmehl bei der BMW Group, sondern der erstmalige Einsatz überhaupt in der Automobilindustrie“, erklärt Dr. Jürgen Stiegler, Leiter der Lackiererei in Regensburg.
Recycling von Lack-Overspray durch das neue Verfahren
Das neue Verfahren ermöglicht das Recycling von Lackoverspray. Alle umgerüsteten Lackierstraßen an den ostbayerischen Standorten der BMW Group arbeiten mit einem Trockenabscheidesystem, das Kalksteinmehl als Bindemittel verwendet. Der Lacknebel, der die Karosserie nicht erreicht, wird statt mit Wasser mit Gesteinsmehl aufgefangen, wodurch der Wasserverbrauch deutlich reduziert wird. In Dingolfing werden so jährlich vier Millionen Liter, in Regensburg 13 Millionen Liter Wasser eingespart.
Die Trockenabscheidung erfolgt zu 80 Prozent im Umluftbetrieb, im Gegensatz zur früheren Nasswäsche. Dadurch müssen nur noch 20 Prozent der Luft temperiert und befeuchtet werden, was zu einer erheblichen Energieeinsparung führt. In Dingolfing sinkt der Heizenergiebedarf um 13.000 Megawattstunden pro Jahr, was einer CO2-Reduktion von mehr als 4.000 Tonnen entspricht. Im Werk Regensburg werden 4.400 Megawattstunden Erdgas pro Jahr eingespart und damit rund 1.150 Tonnen CO2 vermieden.
Ein weiterer Vorteil der neuen Lackieranlage: Das Kalksteinmehl muss nicht als belastetes Abwasser behandelt und entsorgt werden, sondern wird in den Wertstoffkreislauf zurückgeführt.
Kalksteinmehl vom Fuße der Walhalla – vom Bindemittel zum Baustoff
Das Kalksteinmehl wird aus der Region bezogen, konkret von Walhalla Kalk, der am Keilberg bei Regensburg abgebaut wird. In Dingolfing werden durchschnittlich drei, in Regensburg ein bis zwei Lkw pro Woche mit frischem Material beliefert. Das Mehl wird in große Silos gefüllt und gelangt von dort staubfrei in die Lackierkabinen.
Pro Fahrzeug werden in den Lackierereien rund 20 Kilogramm Steinmehl als Bindemittel eingesetzt, das anschließend recycelt und unter anderem als Rohstoff für die Zementproduktion verwendet wird. Damit leisten die Lackierereien einen zusätzlichen Beitrag zur Baustoffproduktion, während sie täglich rund 2.850 Rohkarossen lackieren.
Mit der Umstellung der Lackiererei geht die BMW Group einen weiteren Schritt in Richtung einer nachhaltigen Zukunft in der Produktion.