BMW Group treibt Innovation mit 3D-Druck voran
Die sogenannte „Additive Manufacturing“ wird seit drei Jahrzehnten von der BMW Group genutzt: Neben einzelnen Komponenten von Fahrzeugen werden mittlerweile auch Werkzeuge und Hilfsmittel im 3D-Druckverfahren hergestellt. Dies bringt in zahlreichen Bereichen verschiedene Vorteile mit sich – unter anderem auch bei der Verwendung von Robotergreifern.
09.01.2025
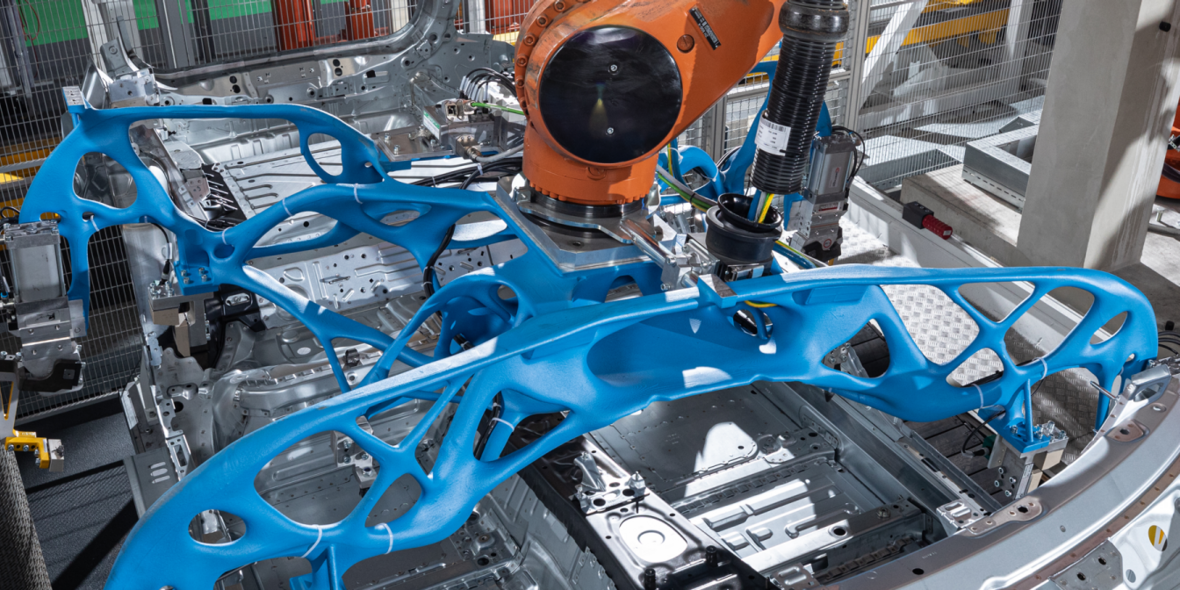
3D-Druck als moderne Tradition
Seit 1991 setzt die BMW Group auf 3D-Drucktechnologie: Damit werden Fahrzeugteile für spezielle Modelle, Konzeptfahrzeuge, Prototypen sowie für Renn- und Serienfahrzeuge entworfen, ebenso wie Werkzeuge für den Bau und die Fertigung in den BMW-Werken. Mittlerweile werden weltweit mehr als 400.000 Teile durch 3D-Druck gefertigt. Diese Produktionsweise stellt insbesondere eine kosteneffiziente und flexible Lösung zur raschen Herstellung von benötigten Einzelteilen dar. Inzwischen hat der 3D-Druck jedoch bereits die Herstellung einzelner Komponenten überschritten – ganze Geräte sind mittlerweile mittels 3D-Druck gefertigt worden.
Die BMW Group erkennt die Vorteile und den Nutzen dieser Technologie und hat sich intensiv damit auseinandergesetzt: Am „Additive Manufacturing Campus“ in Oberschleißheim wird Forschung und Produktion der Technologie unter einem Dach vereint. Allein im Jahr 2023 wurden dort über 300.000 Teile in Oberschleißheim hergestellt, ergänzt durch zusätzliche Produktionen im globalen Netzwerk der BMW Group.
„Der vermehrte Einsatz von Additive Manufacturing im BMW Group Produktionssystem bringt zahlreiche Vorteile. Wir sind damit zum Beispiel in der Lage, selbst Produktionshilfsmittel und Handling-Greifer zu produzieren, die wir jederzeit individuell an die Bedürfnisse anpassen und dazu gewichtsoptimiert gestalten können. Weniger Gewicht ermöglicht höhere Geschwindigkeiten am Band, verkürzte Taktzeiten und reduzierte Kosten. Außerdem können mittelfristig kleinere Roboter eingesetzt werden, was ebenfalls CO2‑Emissionen und Kosten verringert“, meint Jens Ertel, Leiter des Additive Manufacturing Campus.
Fortschritt vorgreifen – die Robotergreifer in den BMW Werken
Der 3D-Druck eröffnet auch in der Produktion umfassende Vorteile. Im Leichtbau- und Technologiezentrum in Landshut wird ein Greifer-Element verwendet, das in nur 22 Stunden gedruckt wurde. Mit einem Gewicht von lediglich 120 Kilogramm kommt dieser Greifer an einer Presse zum Einsatz, die für die Herstellung von CFK-Dächern für die BMW M Modelle verantwortlich ist. Durch den Einsatz des 3D-Drucks konnten rund 20 Prozent des Gewichts eingespart werden, was dazu führt, dass der Robotergreifer sowohl robuster als auch langlebiger ist und die Wartungsintervalle der Anlage verkürzt werden konnten. Das 3D-Druckverfahren LSP (Large Scale Printing) ermöglicht eine nachhaltigere Produktion großer Bauteile. Die Kombination aus Spritzgussgranulat und recyceltem Kunststoff sowie CFK-Reststoffen reduziert den CO2-Ausstoß bei der Herstellung des Robotergreifers um mehr als 60 Prozent.
Seit dem Jahr 2023 kommen neue, noch leichtere Greifer zum Einsatz – diese bionischen Robotergreifer sind topologisch optimiert und sparen zusätzlich 25 Prozent an Gewicht ein. Dadurch kann die Fertigung der CFK-Dächer nun mit nur einem einzigen Greifer anstelle von dreien durchgeführt werden. Die Doppelgreifer werden alle intern im BMW Group Werk Landshut durch das 3D-Druckverfahren individuell gefertigt.
In weiteren BMW Group Werken in Deutschland finden ebenfalls 3D-gedruckte Hilfsmittel im Karosseriebau Anwendung. In München beispielsweise sind bionische Robotergreifer im Einsatz, die die gesamte Bodengruppe eines BMW i4 greifen und bewegen können. Diese neue Generation von Greifern wurde hinsichtlich Gewicht und maximaler Traglast weiter optimiert – jeder Greifer wiegt in seiner endgültigen Form nur noch etwa 100 Kilogramm, was eine Gewichtsreduzierung von 30 Prozent im Vergleich zum Vorgängermodell darstellt. Die filigrane Struktur wird durch eine Mischung aus Sandguss und Aluminium ermöglicht und kann für Schwerlastroboter eingesetzt werden, die weniger Energie verbrauchen und somit auch die CO2-Emissionen senken.
Optimiert von Hardware zur Software
Der ideale 3D-Druck erfordert eine präzise Planung und Berechnung der Strukturen. Innovative Softwarelösungen wie Synera, früher bekannt als Elise, ermöglichen dies – nach intensiver strategischer Entwicklung durch BMW iVentures wird Synera mittlerweile in zahlreichen Bereichen der BMW Group verwendet. Die Software steigert die Effizienz bestehender Prozesse und Berechnungen und ermöglicht so den nahezu identischen 3D-Druck von bionischen Strukturen entsprechend dem entworfenen Design.
Insbesondere im Additive Manufacturing Campus in Oberschleißheim wird die Software kontinuierlich weiterentwickelt. Ein Team aus Fachleuten für Design und Konstruktion analysiert verschiedene Softwareanwendungen und identifiziert dabei zusätzliche Optimierungsmöglichkeiten. Auch für die BMW 3D-Drucker, die für die Herstellung von Robotergreifern zuständig sind, wurden Lösungen erarbeitet, um die Konstruktion der Materialstruktur zu automatisieren, was ein gezielteres und somit schnelleres Drucken ermöglicht.